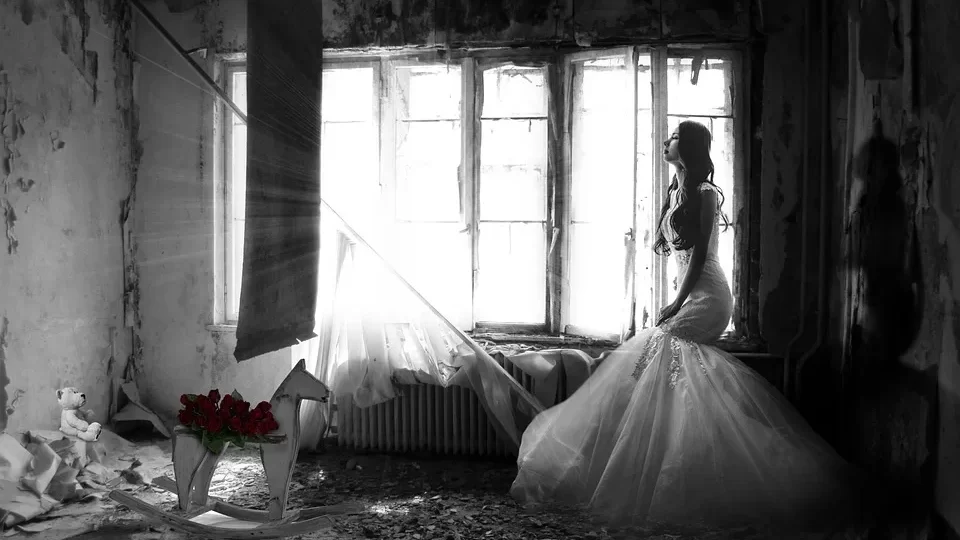
The Fate of the Beam Drill Line
For structural steel suppliers – those who cut, weld, shape and create joists, trusses and beams for high rise building, industrial facilities, power plants, convention centers – the definition in automation in the last decade has been the CNC beam drill line. A beam drill line is a machinery system that uses a conveyor to move a steel beam or “girder”into position, then drills holes – namely bolt holes – in multiple locations along the steel piece, according to the instructions provided in an engineering drawing of what the end product is to be.
An automated beam drill line is a big productivity boon, compared to the conventional way of making numerous measurements on the bare beam to mark it according to the paper drawing instructions, then drilling the holes manually – typically using a heavy duty drill press. This, of course, was an all manual process.
The modern beam drill line can digest the digital drawing file, figure out where the holes are to be placed, “probe” the beam using positioners, sensors and the drill head itself, then drill through the steel at impressive speeds using super-hard carbide drill bits and cooling fluids. The bolt holes are made in very little time and most of the human effort is getting the steel workpieces on and off the line and downloading the drawing file into the machine’s control system.
That’s a huge advantage over the “old fashioned” method, but there’s one catch, and it’s a big one. THERE ARE OFTEN QUITE A FEW MORE MANUFACTURING OPERATIONS THAT MUST BE DONE ON THE STEEL BEAM. Cutting various shapes (for example copes, notches, bevels) into the beam, trimming off the end of the section to get it to the specified length, and “burning” different characters and symbols into the section are additional operations typically required on many steel beams. None of these operations can be performed by a beam drill line.
In summary, while a beam drill line boosts productivity of drilling bolt holes, it doesn’t automate any of these other tasks.
A radically different fabrication method has come to this industry from the plate fabrication trade that performs drilling operation as fast and as precisely as the beam drill line, but brings this same level of automation to all the other cutting and engraving tasks performed on steel beams. The new method uses high-definition plasma cutting to thermally cut through or scribe the beam.
This technology is similar to the beam drill line in that the structural section is transferred into the plasma torch vicinity, the digital drawing file is loaded into the plasma machine’s PC-based control system, and the cutting torch tip touches the workpiece to figure out (and remember) exactly where it is in 3D space and what all of its various features are. Then the plasma torch goes to work making not only bolt holes, but notches, slots, copes and trim cuts . . . the complete list of features customers demand of structural steel suppliers.
The automated plasma cutting machines can produce all these needed features, going from one side of the beam to the other side. When it’s done, all the needed operations are finished – there’s no need to transfer the finished beam to a downstream process. In a way, the new plasma technology is a “full-service” suite for structural steel suppliers.
Different versions of these plasma machines are coming on the market, with a variety of capacities and prices. One thing seems for certain, though . . . the best days for beam drill line technology are in the rearview mirror.
Line
#Fate #Beam #Drill #Line
Will be pleased to have you visit my pages on social networking .
Facebook page here.
Twitter account is here.
Linkedin account here
Post byBedewy for info askme VISIT GAHZLY