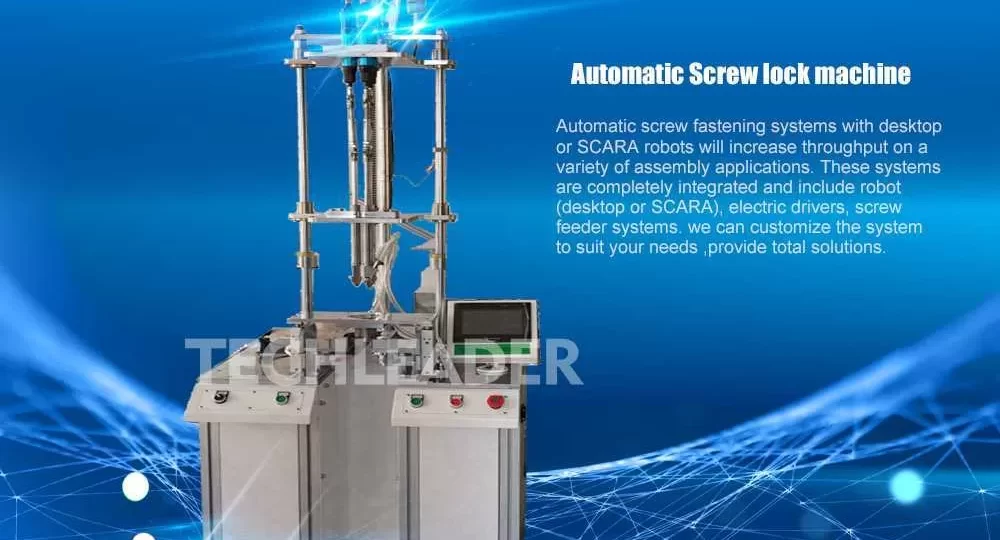
The customization process of a whole screwing machine is done based on a lot of factors. In this article, we are going to take a look at the customization of the automatic screw machine on the basis of the product of the customer. Read on to find out more.
1. First of all, the company gets in touch with the customer in order to find out and confirm the demands of the customer. Apart from this, they also ask the customer for the actual samples.
2. The R&D department of the project organizes a special team in order to perform a basic analysis of the product’s internal structure and provide a fundamental solution for the production line.
3. The engineer takes part in the discussions that allow the exchange of information. During these discussions, the customer may ask for the required details about the machine they need.
This allows the project team to get professional answers. Also, if a customer feels the need to change a specific part of the machine, the engineers can perform the feasibility evaluation first. Afterward, they keep the discussions going to reach a decision.
4. After detailed discussions, the final solution is agreed upon.
5. After the confirmation of the solution, the concerned parties sign the contract. Once the contract has been signed, the company may ask for advance payment for the automatic screw locking machine.
6. The supplier will make arrangements for a special team to put together and supply the drawing to the concerned production department. The next phase involves the production stage.
7. Once the assembly line is ready, the production moves to the trial phase until the debugging process is started.
8. After the clearance of the trial operation, the quality check sends a confirmation that the entire screwing machine has been shipped. In the meantime, the customer is sent a reminder to make the remaining payment.
9. After the final payment has been made according to the payment terms, the customer can receive the delivery.
10. Once the customer has received the machine, the supplier can ask their engineers to reach the customer to offer after-sales service. This includes the installation of the machine as well as the debugging process. During this process, any problems with the machine can be fixed to ensure that the machine is working fine.
11. After the debugging process, the production phase begins. The supplier can offer technical support for years to come. The customer is required to get the balance payment based on the contract terms.
The Scope of these Machines
Primary, non-standard customized machines are designed and made based on the requirements of the customer. During the design phase, suppliers consider the uses of the machine to ensure it will serve the required purpose.
So, this was an introduction to the customization of the screw tightening machines. If you are looking for these machines, make sure you consider these details. This will help you make sure that you get the best machine.
AUTOPOST by BEDEWY VISIT GAHZLY